SPONSORED
Kee Safety, Inc. - Branded Feature
Building Safety: From Compliance to Culture
Workplace safety is a cornerstone of operational success for facility professionals. Beyond meeting regulatory requirements, fostering a culture of safety enhances employee well-being, boosts productivity, and reduces operational risks. This article, inspired by Kee Safety, Inc.’s white paper "Industry Insights: From Compliance to Culture," explores practical strategies to elevate safety from a checklist of obligations to a deeply ingrained organizational value. Facility managers, safety officers, and leadership teams can use these insights to create safer, more resilient workplaces.
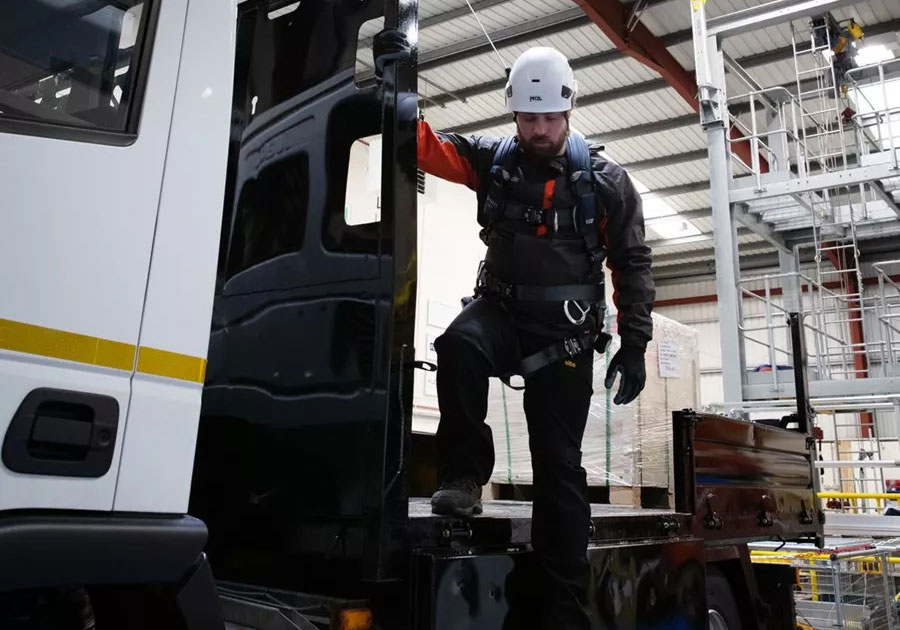
The Importance of Safety Compliance Compliance with safety regulations, such as those set by the Occupational Safety and Health Administration (OSHA), is the foundation of any workplace safety program. OSHA’s standards cover a wide range of hazards, from fall protection to machine guarding, and non-compliance can result in fines, legal liabilities, and reputational damage. For instance, in 2024, OSHA issued over $150 million in penalties for safety violations, with fall-related incidents being the leading cause of workplace injuries.
Compliance ensures that minimum safety standards are met, but it is only the starting point. Facility professionals must stay informed about evolving regulations, conduct regular audits, and invest in training to maintain compliance. For example, ensuring that guardrails meet OSHA’s 42-inch height requirement or that workers are trained in proper harness use can prevent costly accidents. However, compliance alone does not guarantee a safe workplace. A reactive approach—addressing safety only when regulations demand it—often fails to address underlying risks or engage employees effectively.
Transitioning to a Safety-First Culture A safety-first culture goes beyond compliance by embedding safety into every aspect of an organization’s operations. This shift requires leadership commitment, employee engagement, and systemic changes. A safety culture is proactive, encouraging workers to identify hazards, report near-misses, and participate in safety initiatives without fear of reprisal. Studies show that organizations with strong safety cultures experience 50% fewer incidents and higher employee retention rates.
Leadership plays a pivotal role in this transformation. Facility managers and executives must model safe behaviors, allocate resources for safety programs, and communicate the importance of safety regularly. For instance, conducting monthly safety briefings or investing in ergonomic equipment demonstrates a commitment to employee well-being. Employees, in turn, need to feel empowered to take ownership of safety. This can be achieved through peer-led safety committees or incentive programs that reward proactive safety behaviors.
Practical Strategies for Building a Safety Culture
- Comprehensive Training Programs Training is the backbone of any safety initiative. Facility professionals should design training programs that are role-specific, interactive, and ongoing. For example, workers in high-risk areas, such as rooftops or warehouses, need specialized fall protection training, while office staff may benefit from ergonomic workshops. Virtual reality (VR) simulations are an emerging tool, allowing workers to practice responding to hazards in a controlled environment. Regular refresher courses ensure that safety knowledge remains current.
Training should also address behavioral aspects of safety. Teaching employees to recognize cognitive biases—such as overconfidence in familiar tasks—can reduce complacency. For instance, a worker who has operated a forklift for years may skip safety checks, increasing the risk of accidents. Behavioral training encourages mindfulness and adherence to protocols.
- Hazard Identification and Risk Assessment Proactive hazard identification is critical to preventing incidents. Facility managers should conduct regular walkthroughs to identify risks, such as unguarded edges, cluttered walkways, or faulty equipment. Tools like Job Safety Analysis (JSA) can break down tasks into steps, identifying potential hazards at each stage. For example, a JSA for ladder use might highlight the risk of uneven surfaces or improper ladder angles.
Employees should be encouraged to report hazards through anonymous reporting systems or mobile apps. Near-miss reporting—documenting incidents that could have caused harm—is equally important. Analyzing near-misses helps identify patterns and implement corrective actions before injuries occur. For instance, if multiple workers report slippery floors in a warehouse, facility managers can invest in non-slip coatings or improve housekeeping practices.
- Safety Technology and Equipment Advancements in safety technology offer new opportunities to protect workers. Fall protection systems, such as guardrails, safety nets, and personal fall arrest systems, are essential for high-risk environments. For example, modular guardrail systems can be installed on rooftops without penetrating the surface, ensuring compliance with OSHA standards while preserving building integrity.
Wearable technology, such as smart helmets or vests with sensors, can monitor worker conditions in real-time, alerting supervisors to fatigue or environmental hazards. Drones are increasingly used for inspecting hard-to-reach areas, reducing the need for workers to enter dangerous zones. Facility professionals should evaluate these technologies based on their workplace’s specific needs, balancing cost with long-term safety benefits.
- Employee Engagement and Communication Engaging employees in safety initiatives fosters a sense of ownership. Safety committees, composed of workers from various departments, can provide valuable insights into workplace risks and solutions. Regular safety meetings or toolbox talks—short, focused discussions on specific safety topics—keep safety top of mind. For example, a toolbox talk on proper ladder use can reinforce training and address recent near-misses.
Recognition programs can motivate employees to prioritize safety. Publicly acknowledging workers who report hazards or suggest improvements reinforces positive behaviors. Conversely, facility managers should avoid punitive approaches, as they can discourage reporting and undermine trust.
- Measuring and Improving Safety Performance Tracking safety metrics provides insight into the effectiveness of safety programs. Key performance indicators (KPIs) include incident rates, near-miss reports, training completion rates, and audit findings. For example, a decrease in lost-time injuries may indicate that safety interventions are working, while an increase in near-miss reports suggests greater employee awareness.
Regular program evaluations help identify areas for improvement. Facility managers should benchmark their performance against industry standards and solicit employee feedback. For instance, surveys can reveal whether workers feel comfortable reporting hazards or if training meets their needs. Continuous improvement ensures that safety programs remain relevant and effective.
Overcoming Common Challenges Building a safety culture is not without challenges. Resistance to change is common, particularly among workers accustomed to old practices. Facility managers can address this by communicating the benefits of safety initiatives, such as reduced injuries and improved job security. Involving employees in decision-making—such as selecting new safety equipment—can also increase buy-in.
Resource constraints are another hurdle. Small organizations may struggle to fund safety upgrades or hire dedicated safety staff. In such cases, facility managers can prioritize high-impact interventions, such as low-cost housekeeping improvements or free OSHA training resources. Partnerships with safety consultants or industry associations can provide additional support.
Sustaining a Safety Culture A safety culture requires ongoing effort to sustain. Facility professionals should integrate safety into long-term strategic planning, ensuring that it remains a priority amid organizational changes. For example, during facility expansions, safety considerations—such as installing guardrails or updating evacuation plans—should be addressed early in the design process.
Leadership transitions can disrupt safety initiatives, so documenting processes and training successors is essential. Regular safety audits and employee feedback loops help maintain momentum. Celebrating milestones, such as achieving a year without lost-time injuries, reinforces the value of safety.
Safety Culture in Action
The Role of Facility Professionals Facility professionals are uniquely positioned to drive safety culture transformation. Their responsibilities—overseeing maintenance, managing contractors, and ensuring compliance—intersect with every aspect of workplace safety. By championing safety initiatives, collaborating with leadership, and engaging employees, they can create environments where safety is a shared value.
Elevating workplace safety from compliance to culture is a journey that requires commitment, creativity, and collaboration. By implementing comprehensive training, leveraging technology, and fostering employee engagement, facility professionals can build safer, more productive workplaces.
Compliance remains the baseline—it’s non-negotiable. But compliance alone won’t solve deep-rooted safety issues or drive cultural change.
A culture-first approach combines rules, systems, and behaviors to build resilient, engaged teams. That means empowering employees, adopting prevention mechanisms, and measuring to sustain progress.
To explore these strategies in depth, download the full "Industry Insights: From Compliance to Culture," at: https://www.keesafety.com/guides/industry-insights-from-compliance-to-culture
Kee Safety, Inc. is a global leader in fall protection and safe access solutions. For over 85 years, Kee Safety has been dedicated to separating people from hazards—providing OSHA-compliant systems that protect workers at height across industrial, commercial, and institutional environments. The company offers a wide range of engineered safety products, including guardrails, lifeline systems, skylight protection, and rooftop access platforms.
Learn more at www.keesafety.com