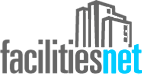
Improved Energy Efficiency and Lower Operating Costs with Modern HVAC Equipment
In the late 1940’s Ed Malzahn invented the first mechanical trenching machine, the Ditch Witch Model DWP Service Line Trencher. From that day forward, Ditch Witch built an entire industry around trenchers to become a leader in utility underground construction equipment. Ditch Witch is a pioneer in all facets of the business, from product design and engineering to manufacturing in state-of-the-art facilities. So when it came time for Charles Machine Works (CMW), Ditch Witch’s parent company, to update the HVAC system at the Ditch Witch product development center, the company wanted a sustainable solution that leveraged renewable resources.
“As a company, we’ve made a living out of serving the underground construction industry, and to stay on top of the latest trends and understand the newest innovations, we figure there isn’t a better way than to install them at our own facilities,” says Tony Guinn, plant engineer for CMW.
At the time, CMW was making several updates to the product development center to improve building energy efficiency and increase occupant comfort. It planned to accomplish this through improved building envelope performance such as replacing window walls with low-e glass and installing a new HVAC system.
Guinn started the HVAC project by doing research on the latest technologies. He worked closely with the International Ground Source Heat Pump Association (IGHSPA) to understand how to upgrade the original chiller-driven system installed in 1978. After implementing several geothermal updates throughout Charles Machine Works facilities, Guinn knew modular chillers that offer simultaneous heating and cooling to reduce energy usage would be the best choice and ultimately lower their operating costs.
Performance above and beyond the typical retrofit CMW turned to Stolhand Heating & Air Conditioning, an HVAC dealer in Oklahoma who was the contractor for the project, to help them find the best modular solution for the application. Darrel Stolhand, owner, recommended specifying three 50-ton ClimaCool Simultaneous Heating & Cooling (SHC) onDEMAND units.
“The project goal was to save money, and a system like this that can blend energy versus just blast heat or cool seemed like the way to get the job done,” Stohland says.
This means instead of throwing away heat the chiller produces, the system recovers it and uses it to heat the building.
The SHC onDemand units were specified as part of a new 150-ton system at the Ditch Witch product development center. The six-header design eliminated extra space in between and around the modules, reducing the overall operating footprint. In addition to the compact design, the unit offers excellent energy savings.
“The SHC onDEMAND modular chiller provides all of the functionality of a traditional boiler/chiller system in a package that saves 75 percent of the average equipment footprint,” says Tom McDermott, director of sales at ClimaCool. “It also has the potential to reduce energy usage by more than 40 percent when compared to traditional boiler/chiller systems. Both factors helped CMW meet their facility upgrade goals.”
The ClimaCool chiller also provided added energy efficiency over traditional chillers due to its ability to use only the energy needed, and nothing more. The modules have individual temperature setpoints improving turndown capacity during changes in occupancy or season. “We locked the thermostats at 73 degrees Fahrenheit to eliminate user fluctuations during last summer’s heat wave, and the system kept the building very cool and comfortable at that temperature,” Guinn says. “We expect that we’ll be seeing about a $50,000 annual savings in operating costs.”
Modern modular chiller provides more than energy efficiency
In addition to increased energy and lowered operating costs, the modern modular chiller also provided unexpected results at the Ditch Witch product development center.
True redundancy: Instead of shutting down the whole system during maintenance, the modular design features separate electrical feeds and dual independent refrigeration circuits, meaning individual modules can be turned off while the rest of the system can continue operating. “This is such an advantage compared to standard chillers, particularly as it means there’s no downtime in the facility when maintenance or other system adjustments are necessary,” explains Stohland.
Easy installation and maintenance: The individual modules fit through standard doorways, simplifying installation. They also are designed with a low center of gravity for easy transport on pallets or forklifts. This design allows service to be conducted by contractors, eliminating the need to access proprietary parts or outside service support that is frequently required with traditional chillers.
With a traditional modular chiller, these benefits would not have been possible. The design flexibility along with the ability to heat, cool or simultaneously heat and cool, and the tailored turndown options have been key to improving energy efficiency and helping Ditch Witch achieve its goal of lowering operating costs without compromising occupant comfort.